


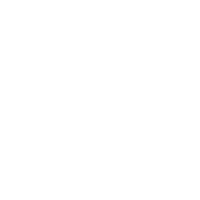
工作经历
2021-02-01 -至今浙江某大型集团公司(上市)项目经理
负责集团及子公司的信息化项目实施落地。 2021年参与集团的省《未来工厂》建设,并成功入选。 2022年负责的集团SCADA项目获《数字化赋能》奖项
2013-07-01 -2020-12-01浙江某软件公司(上市)项目经理
有7年乙方软件公司信息化项目经验,带领团队前后实施了几十家中大型企业的信息化建设.
教育经历
和TA聊聊APP扫码和程序员直接沟通

该用户选择隐藏教育经历信息,如需查看详细信息,可点击右上角“和TA聊一聊”查看
技能
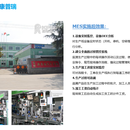
1.设备实时监控,设备OEE分析 对生产线设备实时状态(开机、停机、空转等)进行监控,对设备OEE进行分析。 2.建立全面的过程管控系统 监测生产过程中的每项操作活动以及过程,使得生产单元有序按时地执行作业指令,规范现场操作流程,强化过程管理和控制,达到精细化管理目的。 3.生产加工进度实时监控 可对流程卡、工单在生产线执行到每道工序的进度进行监控。 4.生产过程可追溯 追溯产品在生产加工过程中的批次、加工人员、设备等各项记录。 5.加工工资自动统计 现场报工后自动生成加工员工的计件工资。 6.生产刀具管理 生产设备用到的刀具加工次数进行自动统计,自动统计刀具寿命,对刀具的使用寿命进行预警。 7.现场异常管理 对加工过程中出现的各种异常,由现场人员及时录入上报,可按设定的上报流程自动发送各种消息提醒各级管理人员,对异常情况进行统计分析。 8.过程质量管理 对生产过程中的首检、自检、巡检数据及时采集录入,现场加工数据由检验确认上报,关健工序加工数量到指定数量时自动预警提醒进行检验,对质量数据进行统计分析,实现主动管理和质量控制的目的。 9.建立实时的数据采集平台 通过对现场设备加装PLC等方式,自动地实时获取加工过程中产生的相关数据,如设备状态、加工数量、加工时间等。 10.自动生成各种看板分析 对加工过程中采集到相关信息如设备状态、加工数量、检验数据、异常信息等相关数据,形成相关统计分析报表,供各级管理人员查看。 过去刀具损耗比约45~5%,目前已经降至3%,计划变更比率也从20%降到10%,从这二个关键指标足以说明,智能化对于成本节约和效率提升已经产生明显变化和效益

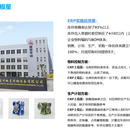
ERP实施后效果: 库存准确率达到了93%以上 库存出入单据时差控制在了4小时以内(上线前需要24个小时)建立企业物料编码与BOM体系; 销售、计划、生产、采购一体化体系建立与迫踪应收应付准确率达到100%;月底结账时间提前5天; 物料控制方面: ERP上线前:仓库的物料库存多,资金占用大,经常出现生产急用的物料没有,不急用的物料很多,占用了场地。 ERP上线后:仓库的库存显示一目了然。采购可以明晰第看到在途物料。仓库可以精准地查询到货位库存。 生产计划方面: ERP上线前:销售部接单之后,对后续的生产无法跟进,生产计划的排程全凭个人经验,缺乏有效的数据参考 ERP上线后:销售部直接将客户订单导入到ERP系统,部门经理审核后,订单自动转到生产计划员的下单界面。生产计划员根据客户订单的订量,结合物料的当前库存、在制量、占用量等数据,计算出车间对应的生产数量。生产计划的排程,根据有效的数据参考,科学合理性大大提升

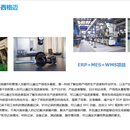
①. 生产线上用宽屏 LED 显示,现场操作和管理人员都可以通过产线线头看板,第一时间了解目前产线的生产进度和作业状况,以及产出和不良等信息。 ②. 公司领导,生产主管,工段长等不同权限人员可以通过车间进度控制,生产日计划,产品进度看板,日计划达成率,产线线头看板等功能,实时了解当天的生产日计划,每日的生产计划达成率,并且可以通过车间进度监控了解车间总体生产进度和状况,可以通过产品进度看板,查询车间成品和半成品情况。 ③. 通过该功能,实现了公司SOP内容显示的无纸化作业,减少了纸张的浪费及时间成本,提高了效率,及准确率,减少由于 SOP 显示内容导致的换线时间。 ④. 能够准确,实时的在 MES 中记录不同工控机的测试数据记录,针对记录的测试数据,可以通过 SPC 功能,自定义 SPC 规则和 SPC 约束实现客户化的 SPC 定制。 ⑤. 对产品的装箱数量,实现了系统管控,不再只是依靠人的记忆解决装箱问题,解决产品的错装问题,并且通过系统能够自动生成装箱条码。 ⑥. 公司可以通过 MES 追溯到生产批号记录情况,材料记录,设备记录,测试数据,操作情况等,可以满足关键信息追溯的要求。
